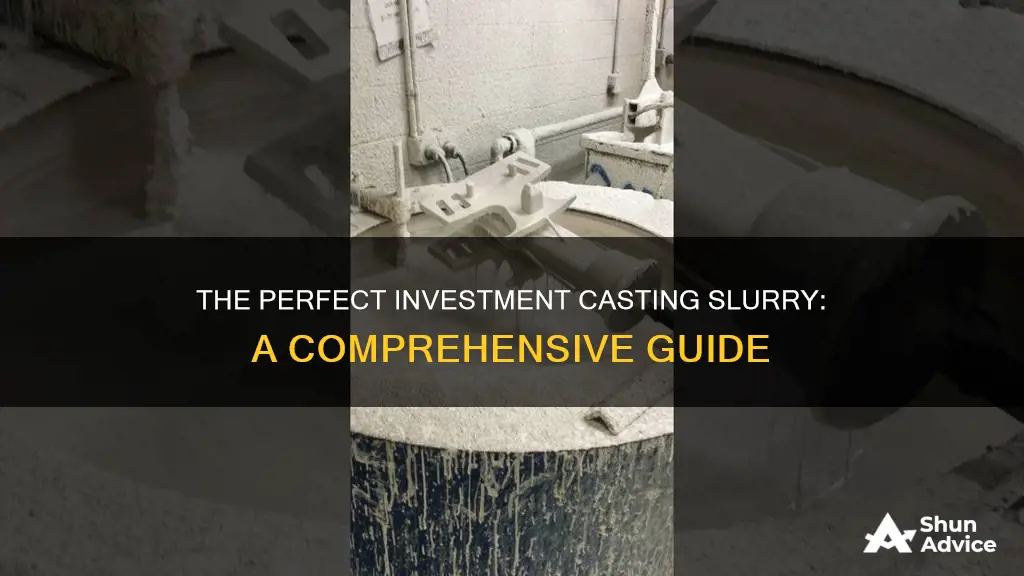
Investment casting is an ancient process, dating back to 4000 BC, that is used to create complex shapes for critical applications. The process involves creating a disposable wax duplicate, also known as the lost wax, which is then dipped into a ceramic slurry and coated with dry refractory grain. The composition of the slurry and refractory grain is determined by the alloys being cast. The dip and coat process is repeated until a shell of sufficient thickness is formed, typically around 3/8 of an inch, to withstand the pressure of wax expansion during dewaxing. The wax is then removed by melting it out, leaving a hollow shell that can be filled with molten metal to form the final product.
Characteristics | Values |
---|---|
Composition | Colloidal silica, zircon flour, fused silica, alumina, welan gum, perlite, Mulcoa 60, frit 3124, corn starch, Kelco-crete, silicon carbide, plaster of Paris, silica sand, etc. |
Consistency | Similar to cake frosting |
Viscosity | Greater than 2500 centipoise |
Application methods | Dipping, brushing, hand packing, spraying, etc. |
Drying time | 4-6 hours |
Drying methods | Air drying, heat exposure |
Shell thickness | Minimum 3/8 inch |
Firing temperature | 1850° F |
Casting metals | Bronze, iron, etc. |
What You'll Learn
The 'lost wax' investment casting process
The Lost Wax Investment Casting Process
The lost wax investment casting process, also known as precision casting or cire perdue, is an ancient technique for creating metal sculptures, dating back over 5500 years. The process involves creating a wax model, coating it in ceramic, melting out the wax, and pouring molten metal into the resulting mould. This method can be used to create intricate works in a range of metals, including silver, gold, brass, and bronze.
Step 1: Model-Making
An artist or mould-maker creates an original model from wax, clay, or another soft material.
Step 2: Mould-Making
A mould is made of the original model or sculpture. This typically involves creating a rigid outer mould and a softer inner mould, which is an exact negative of the original model. The inner mould is usually made of latex, polyurethane rubber, or silicone, supported by the outer mould, which can be made from plaster, fibreglass, or other materials.
Step 3: Wax
Molten wax is poured into the mould and swished around until an even coating is created. This process is repeated until the desired thickness is reached. Another method is to fill the mould with wax and let it cool until the desired thickness has set on the surface. The rest of the wax is then poured out, and the mould is turned upside down to let the wax layer cool and harden.
Step 4: Removal of Wax
The hollow wax copy is removed from the mould. Multiple copies can be made from a single mould.
Step 5: Chasing
The hollow wax copy is "chased" a heated metal tool is used to rub out the marks where the pieces of the mould came together. The wax is dressed to hide any imperfections, so that it looks like the finished piece.
Step 6: Spruing
The wax copy is sprued with a treelike structure of wax that will eventually provide paths for the molten casting material to flow and for air to escape.
Step 7: Slurry
The sprued wax copy is dipped into a slurry of silica, then into a sand-like stucco, or dry crystalline silica of a controlled grain size. This process is repeated until a shell of the desired thickness covers the entire piece. The shell is then allowed to dry.
Step 8: Burnout
The ceramic shell-coated piece is placed in a kiln, where the heat hardens the silica coatings into a shell, and the wax melts and runs out. The shell is then heated further to remove any residual wax.
Step 9: Testing
The ceramic shell is cooled, then tested to ensure that water will flow freely through the feeder and vent tubes. Any cracks or leaks are patched.
Step 10: Pouring
The shell is reheated in the kiln, then placed cup-upward into a tub filled with sand. Molten metal is poured into the shell, which must be hot to prevent shattering.
Step 11: Release
Once the metal has cooled, the shell is removed by hammering or sandblasting.
Step 12: Metal-Chasing
The casting is worked until any signs of the casting process are removed, so that it looks like the original model. Pits left by air bubbles and stubs from the spruing are filed down and polished.
Equity Shares: Investing in Rajiv Gandhi's Vision
You may want to see also
The ceramic shell
Next, the wax tree is coated in a slurry, a mixture of liquid binder and flour refractory materials. Binder and flour materials used vary depending upon the alloy being cast, drying time requirements and the number of coats desired. Once the tree is dipped in the slurry material and excess material is drained from the tree, it is then coated with sand, or stucco. This can be completed in a variety of methods including rainfall sanding, use of a fluidized bed or by hand covering (the cat box method).
After each layer dries, the dipping and stuccoing steps are repeated and continue until the shell is completed. The number of coats will vary depending in part on the pattern configuration and the binder used in the slurry. Once the dipping sequence is completed and each coat has air-dried sufficiently, the wax is removed from the mould with either an autoclave or a FlashFire dewax system; this will melt the wax out of the shell, leaving a hollow cavity.
The shell is then placed into an oven where it is fired for a predetermined time period. This assists in strengthening the shell and removing any remaining wax residue from the inside of the shell. Finally, the fired shell is placed in a bed of sand with the pour cup opening facing up. Molten metal is poured into the shell. The shell takes on the orange glow of the metal and eventually turns white as the metal cools. The shell is then removed, and the parts are cut off of the tree.
Debt or Equity: Navigating Investment Options for Maximum Returns
You may want to see also
Removing the wax
The wax must be removed from the ceramic shell before casting can begin. This is known as the dewaxing process.
The wax is melted out of the shell, leaving a void in the shape of the model. This can be done in a kiln, where the wax is melted and drained out of the bottom of the shell. The kiln temperature is raised over a period of time, from 300°F to 1350°F.
Alternatively, an autoclave can be used to remove the wax. The parts are loaded into a pressurised vessel, which is then filled with steam. This causes the wax to melt and drain away. This method is preferable as it reduces the risk of creating pyrolitic carbon, which can be left behind in the shell and cause issues during casting.
The wax that is drained from the shell can be reclaimed, cleaned, and reused.
Once the wax has been removed, the shell is ready for the casting process to begin.
Emerging Growth Equities: A Guide to Smart Investing
You may want to see also
Filling the ceramic shell with molten metal
Before the shell is filled with molten metal, a thin-walled ceramic mould is created over a pattern of the desired object. This pattern is made from a combustible substrate, such as wax, polystyrene, plastic, or synthetic rubber, which can be melted or burned out of the shell.
The ceramic shell is formed by dipping the pattern into a slurry of liquid refractory binders and then coating it with refractory powder. This process is repeated several times to build up the thickness of the shell and ensure it can hold the molten metal without cracking or leaking. The shell is then dried and the pattern is removed through melting or burning.
Once the shell is ready, it is filled with molten metal, which is then allowed to cool and solidify. Finally, the shell is removed to reveal the desired object.
The entire process, from the application of the shell material to the filling of the shell with molten metal, can be completed within 24 hours, and sometimes in as little as six hours. This "pattern-to-pour" cycle time is significantly shorter than traditional investment casting methods, which can take 24 hours or more just to build up the shell.
Understanding Managed Investment Schemes: Who's Responsible?
You may want to see also
Removing the shell
Once the wax has been melted out of the ceramic shell, the shell is fired in an oven to strengthen it and remove any remaining wax residue. The shell is then placed in a bed of sand, and the molten material is poured into the shell.
After the metal has cooled and solidified, the shell is removed. Methods used to remove the shell can include a hammer, vibration table, high-pressure water blasts, chemical solvents, or a knockout machine. The shell is held in position to ensure uniformity of the removal process.
Inconsistencies in shell thickness can cause havoc and lead to casting defects, but these processes are now accomplished by highly programmable robotic machines. They are extremely reliable and can operate 24 hours a day, seven days a week.
Finally, any additional cleaning and processing steps are then performed to furnish a completed investment casting that meets all the customer's expectations.
Invest in US ETFs: A Guide for Indians
You may want to see also
Frequently asked questions
Investment casting is a process that involves creating a thin-walled ceramic mould around a previously formed pattern of the desired object. The mould is then filled with molten metal and allowed to solidify. After the metal has cooled, the mould is removed to reveal the cast.
Investment casting can be used for casting a variety of metals, including bronze, aluminium, iron, and steel.
A slurry is a mixture of liquid refractory binders that is used to coat a pattern or assembly during the investment casting process. The slurry is then coated with refractory powder or sand to form a shell.
Materials that can be used to make an investment casting slurry include colloidal silica, zircon flour, fused silica, alumina, plaster of Paris, and perlite.