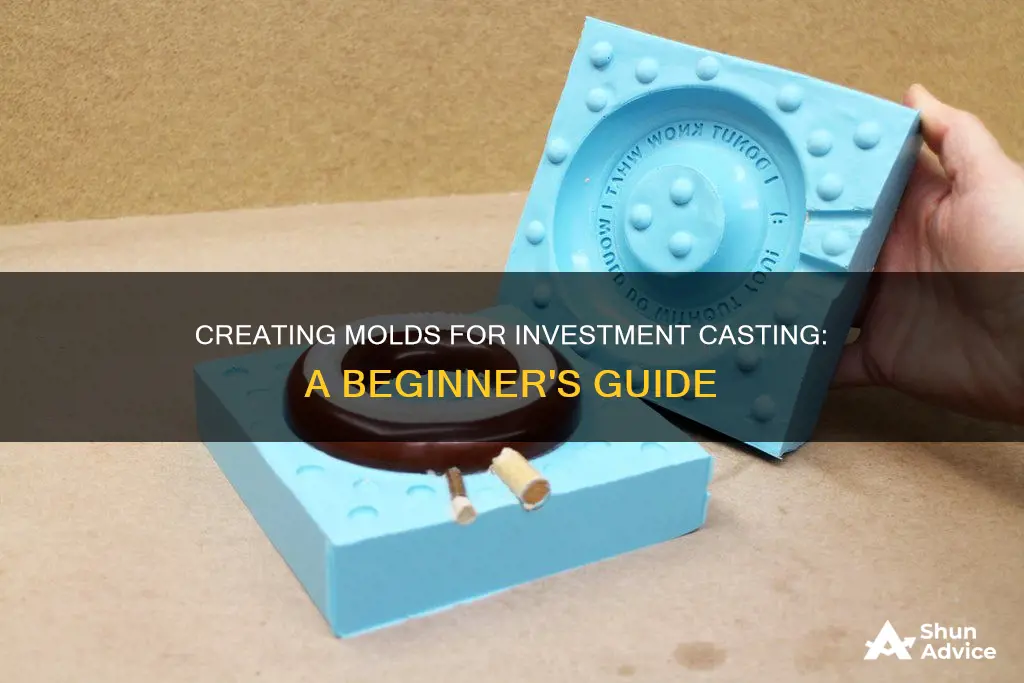
Investment casting, also known as precision casting or lost-wax casting, is a metal casting process that uses a wax pattern to create complex shapes with high accuracy and a smooth finish. The process involves creating a wax pattern, which is then assembled onto a tree with other wax patterns. This tree is then dipped into a ceramic slurry and coated in layers to form a shell. The wax is then melted out, leaving a cavity that can be filled with molten metal. The metal solidifies, and the ceramic shell is broken away to reveal the final product. This process is ideal for creating intricate parts with high precision and a smooth surface finish, but it is more time-consuming and expensive than other casting methods.
Characteristics | Values |
---|---|
Process Name | Investment Casting, Lost Wax Casting, Precision Casting |
Process Description | A metal casting process that uses a wax pattern to create intricate parts with high accuracy and a smooth surface finish |
Process Steps | 1. Create a wax pattern, 2. Assemble wax patterns onto a "tree", 3. Dip the tree in ceramic material and melt out the wax, 4. Pour molten metal into the cavity, 5. Break away the ceramic shell |
Pros | High dimensional accuracy, Smooth surface finish, Ideal for small castings and low-volume production, Great for intricate and complex shapes |
Cons | Non-reusable mould components, Time-consuming and multi-step process, Not suitable for large or heavy parts, Expensive for high-volume production |
Typical Applications | Jewellery, Aerospace components, Dental fixtures, Gears, Turbine blades, Firearm components |
What You'll Learn
Wax patterns
Complex patterns are often assembled from multiple pieces, allowing for the inclusion of cores that will remain in place after the wax is melted to create voids in the metal part. A wax sprue or runner system is attached to each pattern to provide a channel for the metal to flow into the mould cavity. To save costs, multiple small parts can be attached to a central sprue to form a "tree".
The wax formulation determines the flow and moulding characteristics, such as viscosity, melting point, and surface finish. The pattern-maker must select the appropriate type of wax to suit the part design while minimising defects and cycle time. The mould tools are often made from aluminium due to the low injection pressures, which makes modifications easier than when working with tool steels.
Creating wax patterns for investment casting requires a balance between speed, temperature, and quality. The cavity must be completely filled, and the wax must set before the mould opens. Increasing the temperature or injection pressure to reduce cycle time can create cavitation defects in the wax, which will appear as defects in the metal part unless repaired.
Understanding Your Investment Portfolio: A Beginner's Guide
You may want to see also
Sprue and tree assembly
Firstly, you need to create a wax pattern. This pattern should be an exact replica of the final product, taking into account any necessary adjustments for thermal contraction (shrinking). Various types of wax can be used, depending on the specific properties required. The wax pattern can be created through several methods, such as forming a gelatin mould around a 3D model, carving and machining a replica out of wax, or using a metal injection die.
Once the wax pattern is ready, it's time to assemble the tree. The tree is a central structure that allows you to cast multiple parts simultaneously. The wax patterns are carefully attached to a central wax sprue, creating a tree-like arrangement. This sprue will act as a channel to guide the molten metal into the mould during the casting process. The number of patterns attached to the tree depends on the size and configuration of the desired final components.
After assembling the tree, you need to coat it with a ceramic material. This can be done by dipping the tree into a ceramic slurry or spraying it with the slurry to ensure an even coating. It is important to apply multiple layers of the ceramic material to create a shell of the desired thickness. The first layer of the coating is crucial as it determines the surface finish and level of detail on the final product.
Once the desired thickness is achieved, allow the coating to dry completely. This step is crucial in creating a hard shell that will retain its shape during the casting process. Place the dried assembly upside down in an oven to melt out the wax. This step ensures that the wax is completely removed from the tree, leaving behind an empty cavity in the shape of the final product.
Now, your sprue and tree assembly is almost complete. The final step is to preheat the ceramic shell to prepare it for the molten metal. Place the shell in a high-temperature oven, approximately 1000°C (1832°F), to cure the ceramic mould. This preheating process ensures that the ceramic shell can withstand the molten metal and creates the optimal conditions for the casting process.
Vanguard's Investment Manager Selection: The Key Criteria
You may want to see also
Ceramic shell creation
The ceramic shell creation process is a widely used technique for producing high-precision metal parts. This process is known as "lost wax casting" and is popular due to its ability to produce high-quality parts with intricate shapes and fine details. Here is a detailed, step-by-step guide on how to create a ceramic shell for investment casting:
Firstly, a wax model or pattern is created, capturing every detail and subtlety of the final piece. This wax model is crucial as it serves as the foundation for the entire casting process, ensuring precision and accuracy. Once the wax model is complete, it is attached to a sprue pole or wax pole, along with several other wax patterns, forming what is known as a "tree". Smaller pieces of wax, called gates, connect each pattern to the sprue. These gates create spaces for the eventual flow of molten metal into the pattern cavities.
Next, the wax tree is coated with a ceramic slurry, a mixture of liquid binder, flour refractory materials, and a binding agent. This step is done by either dipping the tree into the slurry or spraying it onto the tree. The desired coating thickness should be enough to bear the weight of the metal without causing excessive cooling. After dipping, the excess material is drained, and the tree is coated with sand or stucco. This can be done through various methods, including rainfall sanding, a fluidized bed, or hand covering.
The layers of coating are built up through repeated dipping and stuccoing until the desired thickness is achieved. The number of coats will depend on the pattern configuration and the binder used in the slurry. Once the desired thickness is reached, the wax is removed from the mold using methods like an autoclave or a FlashFire dewax system, leaving a hollow cavity.
The shell is then fired in an oven to strengthen it and ensure the removal of any remaining wax. After this step, the fired shell is ready for preheating and metal pouring. It is placed in a bed of sand with the pour cup opening facing upwards, and molten metal is poured into the shell. The shell takes on an orange glow, which eventually turns white as the metal cools. Finally, the shell is removed, and the parts are cut off the tree, revealing the metal casting.
The ceramic shell creation process is intricate and requires careful attention to detail. It is an excellent method for achieving high-precision, intricate metal castings with a smooth surface finish.
DHFL NCD Investment: Where to Invest in India
You may want to see also
Melting out the wax
Firstly, it is important to understand the investment casting process up to this point. You should have already created a wax pattern, an exact replica of your desired final product, and assembled it onto a "tree" with other wax patterns. This tree is then dipped into a ceramic slurry and coated with layers of ceramic material to create a thick shell.
Now, to melt out the wax, place the ceramic shell upside down in an oven or furnace. The specific temperature may vary, but it should be high enough to melt the wax. This step will depend on the type of wax used, so ensure you are using the correct temperature for your chosen wax. During this process, the wax will melt and flow out of the ceramic shell, leaving behind an empty cavity.
It is important to note that you should place the shell in a steam autoclave before placing it in the oven to remove most of the wax. This will help ensure that all the wax is removed and that the shell is ready for the next step.
Once the wax has melted and flowed out, you will be left with a ceramic shell with cavities in the shape of your desired final product. This shell is now ready for preheating and metal pouring. Be careful when handling the hot shell, and ensure that you are wearing appropriate protective gear, including heat-resistant gloves and safety goggles.
Finally, you can begin the metal pouring process. Heat your chosen metal to a molten state and carefully pour it into the cavities of the ceramic shell. Ensure that the metal completely fills the cavities to create an accurate casting. Once the metal has been poured, allow it to cool and solidify before removing the ceramic shell to reveal your final product.
Workplace Savings and Investment Plans: What You Need to Know
You may want to see also
Pouring metal into the mould
Now that your mould is ready, it's time to pour in the molten metal. This process will vary depending on the type of metal you're using and the complexity of your object, but here are some general guidelines to follow:
Firstly, make sure you are wearing the appropriate safety gear, including heat-resistant gloves and protective eyewear. You will be working with extremely hot materials, so taking the necessary precautions is crucial.
Prepare your molten metal. The type of metal you use will depend on the specific object you are casting. Common metals used in investment casting include stainless steel, superalloys, nickel-based alloys, and copper-based alloys. Heat your metal to its melting point, ensuring it is molten and ready to be poured.
Place your mould in a secure location, such as a workbench, and ensure it is level. If your mould has multiple parts, make sure they are securely fastened together.
Carefully pour the molten metal into the sprue hole of your mould. Use a ladle or another suitable tool to control the flow and avoid splashing. Fill the cavity until it is completely full. Take caution to avoid spilling any molten metal outside the mould, as it can cause injuries or damage to your workspace.
Once the cavity is filled, stop pouring and allow the metal to cool. Depending on the size and thickness of your object, this process can take at least 20 minutes or longer. Do not disturb the mould during this time to avoid any accidental deformation.
After the metal has cooled and solidified, you can begin the process of removing it from the mould. Carefully break away the mould material, taking care not to damage the casting. For ceramic moulds, this can be done using water jets, vibration, or other appropriate methods.
Finally, remove any remaining support structures or gating systems from your casting. This may involve cutting or grinding away the excess metal. Your casting is now complete and ready for any additional finishing processes, such as heat treatment, machining, or polishing.
Stress Testing Your Investment Portfolio: Strategies for Success
You may want to see also