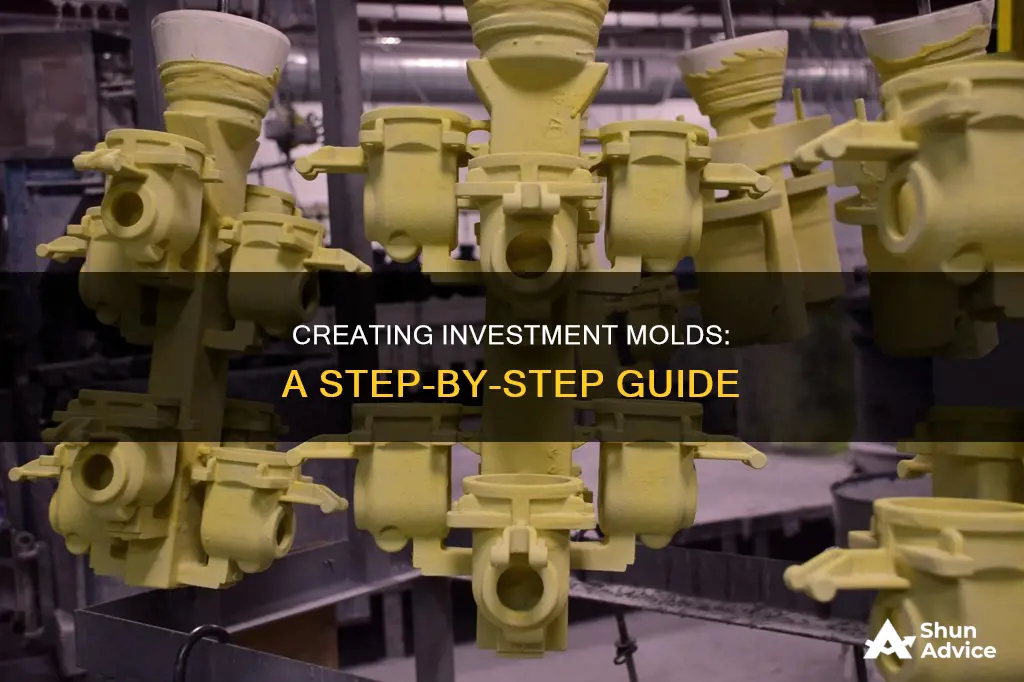
Investment casting, also known as precision casting or lost-wax casting, is a manufacturing process that uses a wax pattern to create intricate parts with high dimensional accuracy and a smooth surface finish. The lost wax process involves coating a wax pattern with a ceramic shell, melting away the wax, and then pouring metal into the shell cavity. This complex, time-consuming, and expensive process can produce small, detailed, and intricate shapes with thin walls and complex internal passageways.
Characteristics | Values |
---|---|
Process Name | Investment Casting |
Other Names | Precision Casting, Lost Wax Casting |
Process | A wax pattern is coated with a ceramic shell, then melted away. Metal is poured into the shell cavity. |
Uses | Creating intricate parts with high accuracy and a smooth surface finish |
Ideal For | Small castings, low-volume production, intricate shapes |
Pros | High dimensional accuracy, smooth surface finish, ideal for small castings, low-volume production |
Cons | Non-reusable moulds, time-consuming, parts can't be too big, expensive for high-volume production |
Materials | Stainless steel, brass, aluminium, carbon steel, glass, bronze, magnesium, etc. |
Steps | Wax pattern production, ceramic mould creation, pouring, solidification, shell and casting removal, finishing |
Wax pattern production
Hot wax is injected into a mould or die and allowed to solidify. The wax pattern is an exact replica of the part to be produced. The method is similar to die-casting, but with wax used instead of molten metal.
A gating system (sprue, runner bars, and risers) is attached to the wax mould. For smaller castings, several wax patterns are attached to a central wax gating system to form a tree-like assembly. A pouring cup, usually attached to the end of the runner bars, is used to introduce molten metal into the mould.
The assembled "pattern tree" is then dipped into a slurry of fine-grained silica. It is dipped repeatedly, with each dip coating the tree with a progressively more refractory slurry. Once the refractory coating reaches the desired thickness, it is allowed to dry and harden, forming a ceramic shell around the patterns and gating system.
The thickness of the ceramic shell depends on the size and weight of the part being cast, and the pouring temperature of the metal being used. The average wall thickness is approximately 0.375 inches (9.525 mm). The hardened ceramic mould is then turned upside down, placed in an oven, and heated until the wax melts and drains away, leaving a hollow ceramic shell.
Forestry Managed Investment Schemes: How Do They Work?
You may want to see also
Ceramic mold creation
Creating a ceramic mold is a fundamental skill in the discipline of ceramics and pottery. It is a process that enables artists and manufacturers to produce precise and consistent replicas of their original designs. The mold captures intricate details and dimensions of the prototype, allowing for the production of consistent ceramic pieces through processes like slip casting.
The first step in creating a ceramic mold is to select the type of mold based on the project's requirements. The most common type is a plaster mold, made from gypsum plaster, which is ideal for slip casting due to its absorbent nature. Other types include silicone molds, used for more complex and detailed designs, and bisque molds, made from fired, unglazed ceramic, which can handle higher temperatures and more rigorous handling.
Once the type of mold is selected, the next step is to prepare the materials and tools needed. These include plaster of Paris for creating the mold, clay to form the initial model, silicone rubber for flexible and reusable molds, and a mold release agent to ensure easy separation of the mold from the model. Essential tools include mixing containers, sculpting tools, brushes, measuring spoons and cups, and wooden frames or coddles to contain the plaster while it sets.
After gathering the necessary materials and tools, the mold-making process can begin. This typically involves the following steps:
- Select a non-porous, well-sealed model to ensure a smooth mold surface. Common materials include clay, plastic, or metal prototypes.
- Prepare the work area by ensuring it is clean and free from dust and debris. Maintain a stable temperature, ideally between 65°F and 75°F (18°C to 24°C).
- Apply a mold release agent to the model, such as PVA or a silicone-based spray, to prevent the ceramic slip from adhering to it.
- Construct a mold box using wooden planks or plastic sheeting, leaving at least one inch of space around the model.
- Seal the edges of the mold box securely with clay or a hot glue gun to prevent leakage when pouring the ceramic slip.
- Mix and prepare the ceramic slip according to the manufacturer's instructions, achieving a smooth and consistent mixture.
- Pour the ceramic slip into the mold box gradually to eliminate air bubbles, ensuring it fully covers the model by at least half an inch.
- Allow the slip to set in the mold box for the recommended time, typically 24 to 48 hours, depending on the slip formulation and room conditions.
- Once the slip has fully set, carefully remove the mold box and extract the ceramic mold. Use non-metallic tools to avoid damaging the mold.
For a two-part ceramic mold, additional steps are required:
- Prepare the model and mold box by securely attaching the model to a smooth surface and constructing the mold box around it, allowing sufficient space for the mold material.
- Apply a release agent to the model and the interior surfaces of the mold box to prevent the plaster from sticking.
- Mix the plaster and pour it into the mold box, covering half of the model. Allow it to set and cure completely.
- Create registration keys (small indentations) in the surface of the mold to ensure precise alignment of the two mold halves.
- Apply another layer of release agent to the exposed plaster surface and the mold box walls.
- Pour the plaster mixture to cover the remaining half of the model, ensuring it fills all spaces evenly. Allow this half to set and cure completely.
- After both halves have dried, gently separate them along the registration keys and remove the model from the mold.
Creating ceramic molds requires precision and attention to detail. Common problems such as insufficient plaster mixture, trapped air bubbles, and sticking or leaking molds can be avoided by following best practices and utilizing advanced techniques. These include using vibrating tables or tapping the mold box to release air bubbles, applying a thin layer of release agent to prevent air bubbles from sticking to the mold surface, and sealing mold seams and joints to prevent leaks.
By understanding the process of ceramic mold creation and utilizing the appropriate materials and tools, artists and manufacturers can produce high-quality molds that capture intricate details and dimensions of their designs. This enables the consistent and accurate reproduction of complex ceramic pieces, revolutionizing the landscape of pottery making.
Crafting a Compelling Investment Narrative: Guide to Portfolio Storytelling
You may want to see also
Pouring
The pouring stage of the investment casting process involves injecting the chosen molten metal into the ceramic mould. This is done while the mould is still hot, so that the liquid metal can flow easily through the thin, detailed sections of the mould. The pre-heated mould also allows the metal to cool and shrink together with the mould, creating a casting with improved dimensional accuracy.
The pouring process begins with the metal being heated to melting point. The temperature will depend on the metal being used, with most common metals being suitable for investment casting, including aluminium, bronze, magnesium, carbon steel, and stainless steel.
The molten metal is then poured into the pouring cup of the mould, and flows through the central gating system into each mould cavity on the tree. The time it takes for the mould to cool into a solid state depends on the material that was cast and the thickness of the casting being made.
Once the casting has solidified, the ceramic moulds are broken down and the casting can be removed. This is usually done manually, or by using water jets. The casting is then separated from its gating system tree using manual impact, sawing, cutting, burning, or by cold breaking with liquid nitrogen.
Equity Investments: Fair Value Reporting Requirements
You may want to see also
Solidification
The solidification stage of the investment casting process involves pouring the molten metal into the ceramic mold and allowing it to cool and harden. This stage is crucial as it determines the quality of the final casting. The time required for solidification depends on the type of metal used and the thickness of the casting.
During solidification, the molten metal is poured into the preheated ceramic mold, which can withstand high temperatures without cracking or deforming. The preheating of the mold ensures a smooth flow of metal into the intricate sections of the mold. It also helps improve the dimensional accuracy of the final casting as the mold and casting cool and shrink together.
The mold is filled with molten metal through a pouring cup attached to the runner bars of the wax gating system. The liquid metal flows through the central gating system and fills each mold cavity. The preheating of the mold ensures a smooth and easy flow of metal, even into the thin and detailed sections of the mold.
After the metal has been poured into the mold, it undergoes solidification. The time required for solidification depends on the type of metal used and the thickness of the casting. The metal cools and hardens, taking on the shape of the mold cavity.
Once the metal has solidified, the ceramic mold is broken down or removed to release the casting inside. This can be done manually or by using water jets. The casting is then separated from the gating system, and any remaining gates and imperfections are removed through processes such as grinding or sandblasting.
The solidification stage is a critical step in the investment casting process, and the quality of the final casting depends on the accuracy of this stage. The precise control of temperature and cooling rate ensures that the metal solidifies uniformly and accurately, resulting in a high-quality final product.
Equities: When Should Clients Take the Plunge?
You may want to see also
Cleanup
Once the metal has cooled and solidified, the ceramic mould shell can be broken away from the casting. The ceramic shell is brittle and can be broken free using water jets, vibration, or other methods. The casting can then be removed from the gating system using manual impact, sawing, cutting, burning, or cold breaking with liquid nitrogen.
Finishing operations such as grinding or sandblasting are often used to smooth the part at the gates and remove any imperfections. Depending on the metal used, heat treatment may be used to harden the final part. Sandblasting is a common method to clean and smooth out metal parts.
The sprue is cut off and recycled. The casting may then be cleaned up to remove any signs of the casting process, usually by grinding. After grinding, the completed casting is then subjected to finishing, which can include removing impurities and negatives by hand tooling and welding. If the part needs additional straightening, this can be done using hydraulic straightening presses.
Life Cycle Theory: Savings and Investment Strategies Explored
You may want to see also