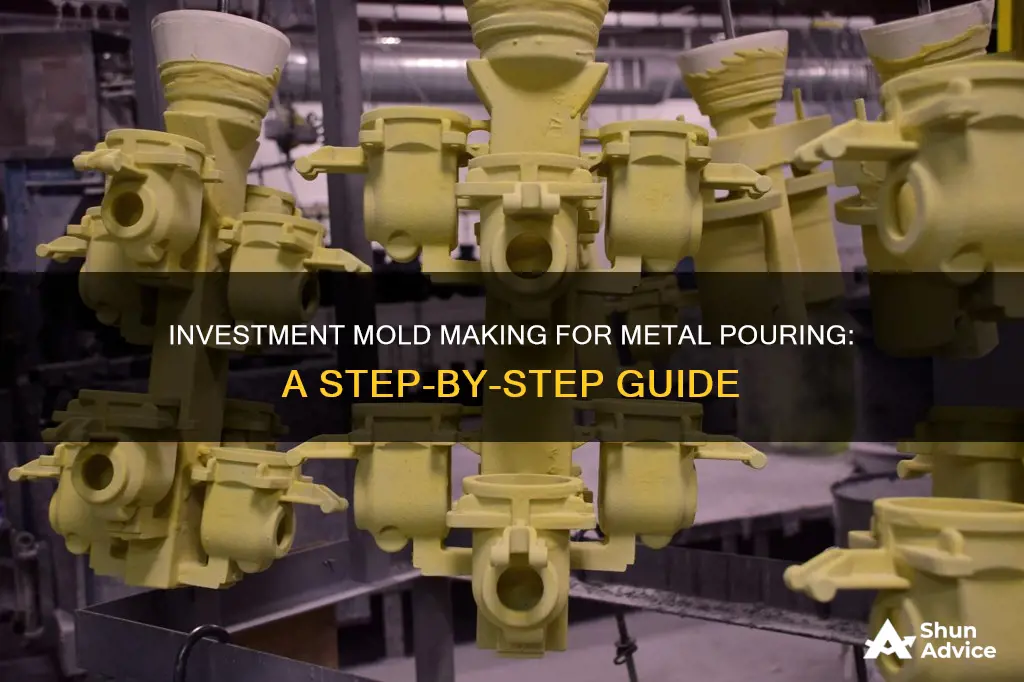
Metal casting is a 7,000-year-old process that involves pouring molten metal into a custom mould to create objects. The type of mould used depends on the type of metal being cast and the desired outcome. For example, sand casting is a popular and inexpensive method for casting aluminium, whereas plaster mould casting is often used for more intricate designs. The process of creating a mould for metal casting involves several steps, from designing the pattern to preparing the materials and assembling the mould. Safety is also a key consideration when working with hot metal.
Characteristics | Values |
---|---|
Materials used for the mold | Sand, plaster, clay, ceramic, kiln-dried plaster, resin-bonded sand, plaster investments, foam, wood, iron, steel, cast iron, aluminium, rubber, silica sand, ethyl silicate, pewter, MDF, cardboard |
Mold type | Expendable/non-reusable, non-expendable/reusable, single-use, permanent |
Mold shape | Two-piece mold frame, drag mold, cope mold |
Mold preparation | Clean and dry sand, apply parting dust, dampen and toss molding sand, fill mold with molding sand, tamp down and scrape off excess sand, flip mold over, repeat for other side of mold |
Mold removal | Break away mold, quench plaster mold in water |
Casting metal type | Aluminium, brass, bronze, pewter, copper, silver, gold, platinum, iron, nickel-based superalloys, titanium, steels |
Casting preparation | Melt metal in a crucible, cover with lid, place in a furnace, wait until last piece of metal melts, wait 3 minutes for aluminium, 5 minutes for brass, 10 minutes for bronze, remove lid, scoop off dross, lift crucible with metal hook, place on iron frying pan, carry to casting mold, pour into mold's sprue hole |
Casting cooling | Allow to cool for 20-30 minutes, shake mold to break up sand, remove object from mold, brush off excess molding material |
Safety equipment | Leather gloves, boots, protective eyewear, goggles, face shield, natural fiber clothing, long pants, long sleeves, insulated gloves |
What You'll Learn
Choose a suitable material for your mould, such as sand, plaster, or ceramic
Choosing a Suitable Material for Your Mould
The type of material you use for your mould depends on the metal you wish to cast, the size of the casting, the level of detail you want to achieve, and your budget. Here are some of the most common materials used for moulds and the considerations for each:
- Sand is a traditional and effective material for moulds. It is commonly used for casting iron and can also be used for metals like pewter and silver. Sand is inexpensive and readily available, making it a good option for larger castings or when you need to create multiple moulds. However, it may not be the best choice for capturing intricate details.
- Plaster is suitable for low-temperature metals and can be used for one-off casts. It is important to use kiln-dried plaster to prevent issues with steam formation during the casting process. Plaster is generally more expensive than sand, but it can provide a smoother surface finish.
- Ceramic moulds are ideal for a wide range of metals and can withstand high temperatures. They are excellent for capturing fine details, making them a popular choice for casting bronze and aluminium sculptures. However, ceramic moulds are typically single-use and need to be broken to remove the cast object.
- Rubber or heat-resistant silicone is suitable for low-melting-point metal alloys. Rubber moulds are flexible and can be used multiple times, making them a cost-effective option for small-scale projects or when casting intricate shapes. However, they may not be suitable for larger castings.
- Metal moulds are an option for low-temperature metals. They are durable and reusable but may be more challenging to work with for complex shapes.
Creating a Diversified Investment Portfolio: Strategies for Success
You may want to see also
Prepare your mould material by cleaning, drying, and mixing with water
Preparing Your Mould Material
Before you begin preparing your mould, you will need to gather your materials. Sand is the primary component for making moulds, so you will need to secure this first. Look for foundry sand that contains silica as this variety can maintain its shape under high heat. You will also need clay, which acts as a binder for the sand. Bentonite and kaolinite are the types of clay that are most commonly used in casting moulds. You will also need a refractory coating, which can be formulated using zirconium silicate, alumina, graphite, or water-based solutions with ceramic particles.
Once you have your materials, you will need to clean and dry your sand thoroughly to eliminate any impurities and moisture that could negatively impact the quality of your mould. Next, you will mix your sand and clay together. You will also need to add water to this mixture. The exact proportions of sand, clay, and water will depend on the specific type of sand and clay you are using, so be sure to consult an expert or a guide specific to your materials.
After your sand, clay, and water are mixed, you will need to let the mixture dry. Again, the drying time will depend on your specific materials, but in general, you should allow this mixture to dry for at least 12 hours before using it to create your mould.
Keynes' Disconnect: Savings and Investment Unhinged
You may want to see also
Create a prototype of your desired object to cast
To create a prototype of the object you wish to cast, you must first decide on the material. Wood or a similar material is a good option for your prototype. This will be your pattern, which will be used to create your mould.
If you are creating an object with two pieces, you will need to create a prototype for each piece.
Your prototype should be an exact replica of the object you wish to cast, but with dimensions that are adjusted to allow for the shrinkage of both the wax and the molten metal. This is important to ensure that your final cast object is the correct size.
If you are using the lost wax method, you will need to create your prototype out of wax. The wax pattern is removed from the tooling and is then coated in ceramic and stucco material. The wax is then melted out, leaving a precisely shaped hollow for your molten metal.
For other casting methods, you will need to create your prototype out of a material that can withstand high temperatures, such as aluminium, steel, or iron. This prototype will be placed in your mould frame and covered with parting dust to prevent the moulding material from sticking.
Make Her Invest in You: Strategies for Deep Connection
You may want to see also
Assemble your mould, ensuring a tight seal
Now that you have created your drag and cope moulds, it's time to assemble them together, ensuring a tight seal. This step involves placing the cope into the cavity of the drag, followed by positioning the cope on top and locking the mould securely into place. Before insertion, the cope needs to be painted, dried, and polished to ensure smooth and precise casting. Once that is done, the assembly process can begin.
Assembling the two halves of the mould is relatively simple and involves only two basic steps:
- Place the cope within the drag, aligning it in the same orientation as it was with the pattern. The cope flask and drag flask should be attached and fixed together to form a tight seal.
- Place clamps or C-clamps around the perimeter of the flask to hold both halves firmly in place.
After the mould has been assembled, the casting process begins. Once it’s completed, the mould needs to be carefully opened and the excess sand gently shaken off. Doing so ensures that the cope can be pulled away from the casting with relative ease. In most cases, the cope is broken off, allowing for easy removal.
The above simple assembly steps complete the mould creation phase. Attention to detail and precision during mould assembly and the other mould-creation steps will significantly contribute to the overall success and quality of the final casting.
Equity Investments: Understanding Their Balance Sheet Impact
You may want to see also
Melt your chosen metal and carefully pour it into your mould
Now that your mould is ready, it's time to melt your chosen metal and carefully pour it into the mould.
First, put on protective gear, including leather gloves, boots, and eyewear. Safety is crucial when working with hot metal. Then, prepare your metal for melting. If you're using aluminium, brass, or bronze scraps, place them in a crucible, cover it with a lid, and put it in a furnace filled with hot coals. Wait until the last piece of metal melts, and then let it sit for a few minutes before pouring: 3 minutes for aluminium, 5 minutes for brass, and 10 minutes for bronze. Do not attempt to melt aluminium products covered with vinyl, such as soda cans.
Once your metal is melted, carefully lift the crucible with thick tongs and place it on an iron frying pan. Use a slotted steel spoon to remove any unmelted metal dross. Then, grab the crucible with the tongs again, and carry it to your casting mould.
Pour the molten metal slowly and carefully into the sprue hole of your mould. Continue pouring until some of the metal starts to come back out of the hole, indicating that the mould is full. If you have any leftover metal, consider pouring it into a steel muffin pan to create small ingots that can be reused later.
Let your mould cool for at least 20 minutes, or longer if your object is larger. Finally, shake the mould to break up the sand and carefully remove your newly-created object. Brush off any excess moulding material, and admire your handiwork!
Equity Group Investments: What's Their Focus?
You may want to see also
Frequently asked questions
Materials used to make an investment mold include sand, plaster, ceramic, clay, kiln-dried plaster, and heat-resistant rubber.
Safety precautions to take when making an investment mold include wearing protective clothing, such as natural fiber clothing, long pants, sleeves, insulated gloves, safety goggles, and a full face shield. It is also important to work in a well-ventilated area and have a chemical fire extinguisher nearby.
To make an investment mold, you will need to create a pattern, make the mold, choose the metallic alloy, melt the alloy, pour it into the mold, and then remove the casting from the mold.