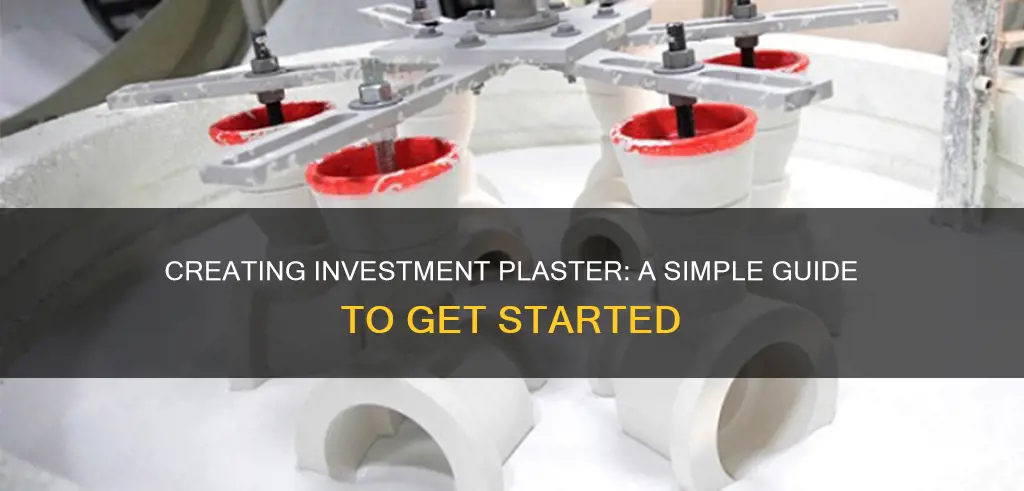
Investment plaster is a material used in casting to create detailed metal parts. It is a manufacturing process used in industries such as aerospace, art, jewellery, and automotive. Investment compounds usually come in powder or concentrated forms and are mixed with water to create liquid moulds that harden around wax models of sculptures. The standard investment for jewellery casting is plaster of Paris because it is excellent at conforming to fine detail when applied in a liquid state and is cheaper than specialised commercial investments. However, it is fragile and loses its bound water at high temperatures. To make investment plaster, one must mix plaster with water at 70 to 72 degrees, using a flour sifter to sift the plaster powder into the water without stirring.
What You'll Learn
- Plaster of Paris is a standard investment for jewellery casting
- Investment compounds are mixed with water to create liquid moulds
- The wax is burnt out to allow molten metal to be poured in
- Plaster investment should be mixed with sand and clay powder to prevent cracking
- Plaster casting is used in industries such as aerospace, art, jewellery, and automotive
Plaster of Paris is a standard investment for jewellery casting
Plaster of Paris is a type of gypsum, and it can be frustrating to use as it loses its bound water at high temperatures. This means that it can be extremely fragile and may turn to dust. However, it is possible to make plaster of Paris more suitable for investment casting with additives. "Real" investment casting plaster is mostly gypsum with a few additives that make it more resistant to heating, such as magnesium oxide and aluminium oxide. Sand or clay are also often added to improve the plaster's ability to set up properly.
When using plaster of Paris for jewellery casting, it is important to mix the plaster quickly but gently, breaking up any lumps that may form. As soon as it starts to thicken, flick plaster onto your sculpture by dipping your fingers into the mixing bowl and flicking them at the model. This helps to drive the plaster into crevices and remove any air. Continue coating your model until the plaster is approximately 1/4-inch thick.
For bronze casting, a rough investment stronger than plaster of Paris alone should be used to avoid cracking due to the high temperature of molten bronze. A mixture of plaster, sand, and clay powder is recommended to create a stronger investment that holds up to heat.
Equity Annuities: Where Your Money is Invested
You may want to see also
Investment compounds are mixed with water to create liquid moulds
Investment compounds are usually sold in powder or concentrated form and are mixed with water to create liquid moulds. The moulds are then used to cast detailed sculptures in bronze, jewellery, and other metal objects. The type of investment compound used depends on the material being cast.
Plaster of Paris is a popular investment compound for jewellery casting because it is excellent at conforming to fine details when applied in a liquid state, and it is cheaper than specialised commercial investments. The water used to mix with the investment compound must be of good quality, as poor water quality can reduce casting quality. The temperature of the water is also important, as it affects the setting rate of the compound.
To create a mould with plaster of Paris, first measure out the water and heat it to 70-72 degrees Celsius. Then, sift the plaster powder into the water using a flour sifter, being careful not to jostle or stir the mixture. Once the water stops absorbing the plaster and starts to crumble at the edges, the mixture has "peaked" and is ready. At this stage, quickly but gently mix the plaster with your glove-covered fingers, breaking up any lumps. As soon as the mixture starts to thicken, dip your fingers into it and flick it onto your sculpture, coating it until the plaster is approximately 1/4-inch thick.
For casting bronze, a stronger investment compound is needed than plaster of Paris alone, as it needs to withstand the temperature of molten bronze without cracking. A mixture of equal parts plaster, sand, and clay powder is recommended, as the silicates in the clay create a stronger, heat-resistant investment.
Investing in US IPOs: A Guide for Indians
You may want to see also
The wax is burnt out to allow molten metal to be poured in
The wax can be melted out using a kiln, an oven, or a microwave. If using a kiln or an oven, place the mould on a tray covered in aluminium foil, with a slight angle so that the wax can pour out. Set the kiln to a slow cone 03 (to burn organics) and the oven to 400°F for 30 minutes. You can tell when the wax has melted out by the smell, but be careful not to let it overheat and catch fire. Alternatively, the wax can be melted out using a propane torch, but be careful not to concentrate the flame, as this will cause the mould to break due to heat stress.
Once the wax has been removed, the plaster mould should be warmed further to remove any remaining water. The mould should also be warm when the metal is poured in, to reduce the temperature difference between the mould and the metal.
Before pouring the metal, ensure you are wearing protective clothing, including eye protection, natural-fibre clothing, long trousers and sleeves, insulated gloves, and safety goggles. Work in a well-ventilated area and ensure you have a chemical fire extinguisher nearby.
A Guide to Investing in Managed Funds
You may want to see also
Plaster investment should be mixed with sand and clay powder to prevent cracking
Plaster investment is a material that comes in powder form and is mixed with water to create a liquid mould. This mould hardens around a wax model of a sculpture, which is then burnt to allow molten metal to be poured in. The standard investment for jewellery casting is Plaster of Paris, as it is excellent at conforming to fine detail when applied in a liquid state.
However, Plaster of Paris is prone to cracking due to the temperature of molten bronze. To prevent this, it is recommended to mix plaster with sand and clay powder. The silicates in the clay create a stronger investment that can withstand higher temperatures. The addition of sand and clay also helps to reduce the cost of the investment, as specialised commercial investments can be expensive.
When mixing plaster with sand and clay powder, it is important to use equal parts of each ingredient. This ensures that the investment has the right consistency and strength. The mixture should be experimental, and you should check the texture of the investment when it dries. If it cracks, add more water, and if it doesn't fully set, use less water.
To further prevent cracking, it is crucial to control the drying process of the plaster. Avoid plastering in direct sunlight or strong wind, as this can cause the plaster to dry too quickly and lead to cracks. The ideal time for plastering is early in the morning when the temperature is cooler and there is less humidity. Additionally, ensure that the wall being plastered is coated with a diluted PVA glue solution. This will prevent the brickwork from absorbing water from the plaster, which can cause it to dry too quickly and crack.
CDs: Investment or Saving?
You may want to see also
Plaster casting is used in industries such as aerospace, art, jewellery, and automotive
Plaster casting is a manufacturing process used to create intricate and detailed metal parts. It is a subset of investment casting, which uses plaster for the casting cavity instead of a refractory (baked ceramic) material. While it is unsuitable for high-volume production due to the fragility of the moulds and the time and cost involved in creating them, it is ideal for producing complex components with a high level of precision. This makes it a popular choice in industries such as aerospace, art, jewellery, and automotive.
Aerospace
Plaster casting is used in the aerospace industry to create lightweight, strong, and relatively low-cost components for aircraft and satellites. The process allows for the production of intricate and detailed metal parts made from alloys such as aluminium and magnesium, which are ideal for applications where weight is a critical factor.
Art
In the world of art and sculpture, plaster casting is a time-honoured technique that allows artists to create detailed, true-to-life reproductions of their original creations. It is a cost-effective method for producing limited editions of sculptures and is also used in architectural applications to create decorative elements.
Jewellery
Plaster casting is commonly used in the jewellery industry to create intricate and detailed metal pieces from precious metals such as gold, platinum, or palladium. The process allows for the production of fine features and high repeatability in moderate production runs, making it a cost-effective method for creating jewellery.
Automotive
The automotive industry utilises plaster casting to create lightweight, strong, and low-cost components for vehicles. Alloys such as aluminium and magnesium are commonly used in automotive applications, taking advantage of their favourable strength-to-weight ratios and relatively low material costs.
Understanding Equity-Based Investment: What Investors Need to Know
You may want to see also
Frequently asked questions
Investment plaster is used for casting metal parts with intricate details and complex shapes. It is suitable for low-melting-point metals and their alloys, such as zinc, copper, aluminum, and magnesium alloys.
Investment plaster casting is similar to traditional investment casting but uses plaster instead of refractory clay. This makes it unsuitable for high-temperature metals like steel and titanium. Sand casting, on the other hand, uses packed or bonded sand and can handle a wider range of metals but typically produces lower accuracy and repeatability. Die-casting uses reusable steel, iron, or carbon cavities and can achieve comparable quality.
Investment plaster can reliably reproduce intricate details and complex shapes with high precision. It delivers excellent surface finishes, reducing the need for post-processing. It is also low-cost and suitable for small to medium production runs. However, it is fragile, labor-intensive, and unsuitable for high-melting-point alloys. Each new pour requires a new mold, and there is a risk of porosity or trapped air in the final cast.
First, create a pattern with sprues, feeders, and gas vents. Set up a mold frame or flask around the pattern, then mix plaster with water to a smooth consistency. Pour the plaster into the flask, minimizing air bubbles. Use a vibrating tool to remove trapped air, and allow the plaster to harden. Burn out the pattern in a furnace, and preheat the mold before casting.
Plaster casting is suitable for low-melting-point metals such as zinc and its alloys, copper and its alloys, aluminum and its alloys, and magnesium and its alloys. It is not suitable for high-melting-point alloys like stainless steel or titanium.