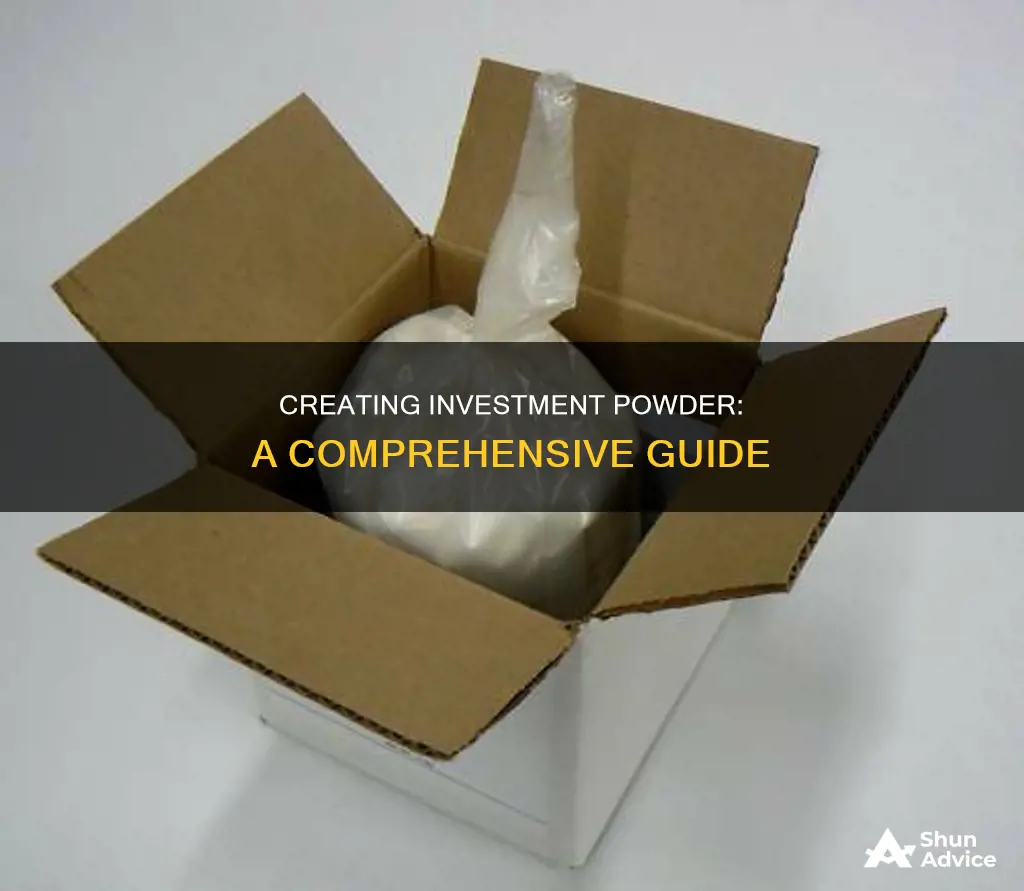
Investment powder is a key component in the casting process, which involves pouring molten metal into a mould to create a range of products, from jewellery to engine parts. The powder is mixed with water to create a slurry, which is then poured into a flask containing a wax tree—a wax model of the object to be cast.
The investment powder mixture must be carefully measured and mixed to ensure a strong mould. The moulds are then heated to remove the wax, leaving a cavity into which the molten metal is poured.
There are various recipes for investment powder, but a basic mixture includes plaster and silica. Other ingredients can be added to improve the powder's performance, including olivine sand, powdered fireclay, borax, and wetting, defoaming, and reducing agents.
Investment powder can be purchased from suppliers, but it can also be made at home. Making your own investment powder allows you to customise the recipe to suit your specific needs and can also help keep costs down, especially when casting large objects.
Characteristics | Values |
---|---|
Main ingredients | Gypsum, silica, plaster, water |
Additional ingredients | Olivine sand, powdered fireclay, borax, cristobalite, limestone, oxidising agents, wetting agents, defoaming agents, debubblizing agents, wollastonite, silicon carbide, sugar, copper powder, carbon, citric acid, soda, dishwashing soap, sodium carbonate, etc. |
Ideal for casting | High-karat gold, fine filigree items, silver, copper, brass, platinum, palladium |
Not ideal for casting | Amethyst, aquamarine, coral, jade, lapis, opal, pearl, peridot, topaz, tourmaline, turquoise |
Working time | 5-15 minutes |
Setting time | 7-15 minutes |
Pour time | Depends on water-to-powder ratio |
Set time | Depends on water-to-powder ratio |
Slump | Depends on water-to-powder ratio |
Green compressive strength | Depends on water-to-powder ratio |
Fired compressive strength | Depends on water-to-powder ratio |
What You'll Learn
Investment powder composition
Investment powder is a mixture of several components, including refractory materials, bonding materials, and controlling chemicals.
Refractory Materials
Refractory materials can withstand high temperatures without decomposing. Silica (silicon dioxide or SiO2) is a common refractory material used in investment powder. It is infusible, meaning it is not melted or changed by the hot metals cast into it. Cristobalite, a mineral of volcanic origin, is another refractory material that can be used. It is created by heating silicas to temperatures between 2680°F and 3040°F (1471°C and 1671°C).
Bonding Materials
Bonding materials hold the refractory materials in place to form a mould. Gypsum (calcium sulphate or CaSO4) is a typical bonding material. When mixed with water, it forms a chemical reaction that results in the bonding material.
Controlling Chemicals
Controlling chemicals are used to control the setting time of the bonding materials and enhance various investment properties. They include wetting agents, which increase the ability of the investment to flow over the wax tree; debubblizing agents, which help remove air from the slurry; and modifying agents, which produce a reducing (anti-oxidation) effect. Modifying agents can include minerals such as copper powder or carbon.
Other Components
Other components may be added to the investment powder to improve its performance or suit specific applications. For example, olivine sand or powdered fireclay can be added for extra refractory properties. Borax can be included to prevent breakage during burnout.
The specific composition of investment powder may vary depending on the intended use and the desired properties. The ratios of the components can also be adjusted to achieve the desired consistency and performance.
Strategic Portfolio Weighting: Key Factors for Investment Success
You may want to see also
Investment powder handling
Storage
Improper storage can reduce casting quality and lead to financial losses. Store investment powder in a cool, dry place, and ensure the storage area is free from contaminants. Keep the powder in its original packaging or airtight containers to prevent moisture absorption and contamination.
Mixing
The water-to-powder ratio is crucial and must be controlled accurately. The standard ratio for jewelry casting is 40% water to 100% investment powder by weight. However, for fine, intricate castings, you can add up to 2% more water to the mixture to improve flow. When mixing, always add the investment powder to the water, not the other way around, to avoid lumps. Mix at a moderate speed for 2-4 minutes, ensuring a smooth, creamy consistency.
Temperature Control
Maintain the temperature of the water and investment powder at room temperature (70°-80° F or 21°-27° C). Higher temperatures will accelerate setting, while lower temperatures may affect casting quality.
Vacuum Application
After mixing, place the slurry under a bell jar and apply a vacuum of 23-27" Hg for 30-45 seconds. Hold the vacuum for an additional 10 seconds before releasing. This process helps remove trapped air, which can cause air bubbles in the final product.
Pouring
Pour the vacuumed slurry into the flask gently, allowing it to flow around the wax tree pattern. Lightly tap the flask during filling to reduce air entrapment. Ensure the pattern is covered by at least 1/2" of investment powder.
Setting
After filling the flask, place it under a vacuum again for 1-2 minutes to remove any remaining air. Allow the flask to set undisturbed for at least one hour for small flasks (2" diameter) and two hours for larger flasks.
Burnout
Remove the sprue base from the flask to expose the wax sprue. Eliminate the bulk of the wax and heat the flask in a kiln or furnace to remove any residual wax and vaporize carbon. For large-scale operations, consider using a steam dewaxer, which removes approximately 90% of the wax before burnout.
Moisture Control
Keep the flasks moist before burnout to prevent the investment powder from drying out. If the investment powder dries out, place the flasks in water for a few minutes or wrap them in wet towels to slowly absorb moisture. Do not heat dry investment powder, as it can crack when heated.
Importing Your Portfolio to Investing.com: A Step-by-Step Guide
You may want to see also
Investment powder mixing
- Water Quality and Temperature: Use de-ionized water to mix with the investment powder. The water quality and temperature play a significant role in the setting time and fluidity of the investment. Contaminants in ordinary tap water can interfere with the chemical reaction between water and plaster, affecting the setting time. Distilled water can also be used to avoid contaminants. The ideal water temperature is between 70° F and 80° F (21° C to 27° C). Higher temperatures accelerate setting, while lower temperatures may affect casting quality.
- Water-to-Powder Ratio: The proportion of water to investment powder should be accurately controlled. Typically, the weight of water is around 40% of the weight of the investment powder. For fine, intricate castings, you can add slightly more water (up to 2%) to improve flow into small crevices. For heavier castings, use slightly less water (around 2% less) to create a sturdier slurry.
- Mixing Procedure: Start by mixing the investment powder with water at a moderate speed in a bowl. Do not add water to the powder, as this can create lumps and make mixing difficult. Mix for 2-4 minutes until the powder is fully incorporated. Then, place the slurry under a bell jar and apply a vacuum of 23-27" Hg for 30-45 seconds. Hold the vacuum for an additional 10 seconds before releasing. This step helps remove trapped air from the slurry.
- Pouring and Vacuuming: Pour the vacuumed slurry into the flask through the side, gently allowing it to flow around the wax tree pattern. Lightly tap the flask during filling to reduce entrapped air. After filling, vacuum the invested flask again under the bell jar for 1-2 minutes to remove any remaining air bubbles.
- Setting and Hardening: Allow the invested flasks to set and harden undisturbed for at least one hour for small flasks (2" diameter) and two hours for larger flasks. After solidification, remove the sprue base to expose the wax sprue and eliminate the bulk of the wax.
- Burnout Process: Heat the flasks in a kiln or furnace to eliminate residual wax and vaporize any remaining water. The burnout temperature and duration depend on the size and type of flask. For smaller flasks, a typical burnout cycle includes heating at 400° F (204° C) for two hours, followed by 850° F (454° C) for two hours, and finally, 1050° F (566° C) for two hours. For larger flasks, extend the duration at each temperature.
- Casting Temperature: After burnout, allow the mold to cool to a temperature below the casting temperature of the metal being cast. For example, if casting sterling silver, cool the mold to around 500° C, which is below the melting point of sterling silver. This ensures that any remaining moisture is eliminated and reduces the risk of defects in the final casting.
By following these instructions and maintaining precise control over the mixing process, you can create high-quality investment molds for casting various metals.
Invest in India: CD Investment Strategies and Tips
You may want to see also
Investment powder setting
The setting process for investment powder is a critical step in the casting process, and improper handling can ruin the final product. The investment powder should be mixed with water in specific ratios, and the temperature of the water and powder should be controlled to ensure optimal results. The working time for the investment powder starts when the powder is added to the water and ends when the flask is filled and left to harden. The mixing process should be done at moderate speed, and the slurry should be placed under a bell jar to remove air bubbles. After vacuuming, the slurry is poured into a flask and allowed to cover the wax tree pattern. The flask is then vacuumed again to remove trapped air, which can cause air bubbles in the final casting.
The setting time for the investment powder can vary depending on the specific product and the temperature. It is important to follow the manufacturer's instructions for the best results. Once the investment powder has been mixed and poured into the flask, it should be allowed to set undisturbed for at least an hour for small flasks and two hours for larger flasks. After the investment has set, the sprue base is removed, and the bulk of the wax is eliminated before heating the flask in a kiln or furnace to burn out the residual wax.
It is important to control the temperature during the burnout process. The flask should be heated slowly to allow the water to turn into steam, which helps eliminate the wax from the mould cavities. If the mould is heated too quickly, it can cause cracks in the investment. The burnout temperature should be high enough to eliminate carbon residue from the wax completely. After burnout, the mould should be cooled to a temperature below the melting point of the metal being cast.
Additional Considerations
- The investment powder mixture should be vacuumed properly to remove air bubbles, which can cause defects in the final casting.
- Distilled water can be used to avoid contaminants from tap water that may affect the investment powder.
- A small amount of commercial retarder can be added to slow down the setting time if desired.
- The investment powder should be stored properly to prevent moisture absorption, which can affect the quality of the castings.
Equity Investment: Understanding Preferred Equity
You may want to see also
Investment powder burnout
- Curing: Allow the investment to bench cure and achieve full green strength after hardening. This is necessary to ensure the investment is hard enough to withstand the expansion of the pattern material during heating. Small flasks should cure for at least an hour, while larger flasks should cure for a minimum of two hours.
- Low-temperature cycle: Remove the bulk of the pattern material at a low temperature, typically between 250-300°F (121-149°C), for 1.5 to 3 hours depending on the size of the flask and the amount of pattern material. This step must be done gradually to avoid spalling, which can result from too high a temperature or insufficient time.
- Ramp-up: Gradually increase the temperature of the moulds to a high-temperature dwell needed to remove carbon. During this cycle, the remaining water is removed from the mould, and it passes through thermal expansion zones. A slow and steady ramp-up rate of around 4°F/minute is recommended to avoid steam and thermal shock.
- High-temperature cycle: The industry standard for removing carbon from the investment is 1350°F (732°C). The duration at this temperature ranges from three to five hours, depending on the size of the flask and airflow. Ensure that the inside of the investment is clean and free of any grey carbon residue, which can lead to gas porosity issues.
- Ramp-down: Investment moulds retain heat well, so allow sufficient time for the mould to cool down. Depending on the flask size, it can take up to two hours to stabilise at the casting temperature. For tall, four-inch-diameter flasks, it is recommended to wait for two hours before casting.
- Casting: After the burnout cycle, the moulds are ready for casting. The casting temperature and timing will depend on the pattern being cast and the alloy used.
It is important to note that improper handling of investment powder can affect the quality of the final product. Factors such as improper storage, poor water quality, incorrect mixing ratios, insufficient mixing methods, and uncontrolled temperatures can reduce casting quality and lead to losses in production and money. Therefore, it is crucial to follow the instructions provided by the investment powder manufacturer and maintain consistent processes to achieve successful results in jewellery casting.
Webull Cash Management: FDIC Insurance Explained
You may want to see also
Frequently asked questions
The basic recipe for making investment powder is 50% plaster with 10-50% silica. Some people also add refractory materials such as olivine sand or powdered fireclay to the mixture.
The ideal water-to-powder ratio depends on the type of casting you are doing. For very fine, intricate castings, you can add slightly more water (up to 2%) to the investment powder to get a finer slurry that flows into smaller crevices more smoothly. For heavier castings, use slightly less water (2% less) with the investment powder for a sturdier slurry.
Some common mistakes to avoid when making investment powder include improper storage, poor water quality, wrong mixing ratios, insufficient mixing methods, and uncontrolled temperatures. These factors can reduce casting quality and cause a loss of production and money.